What You Should Know: Steel Buildings vs Fabric Buildings
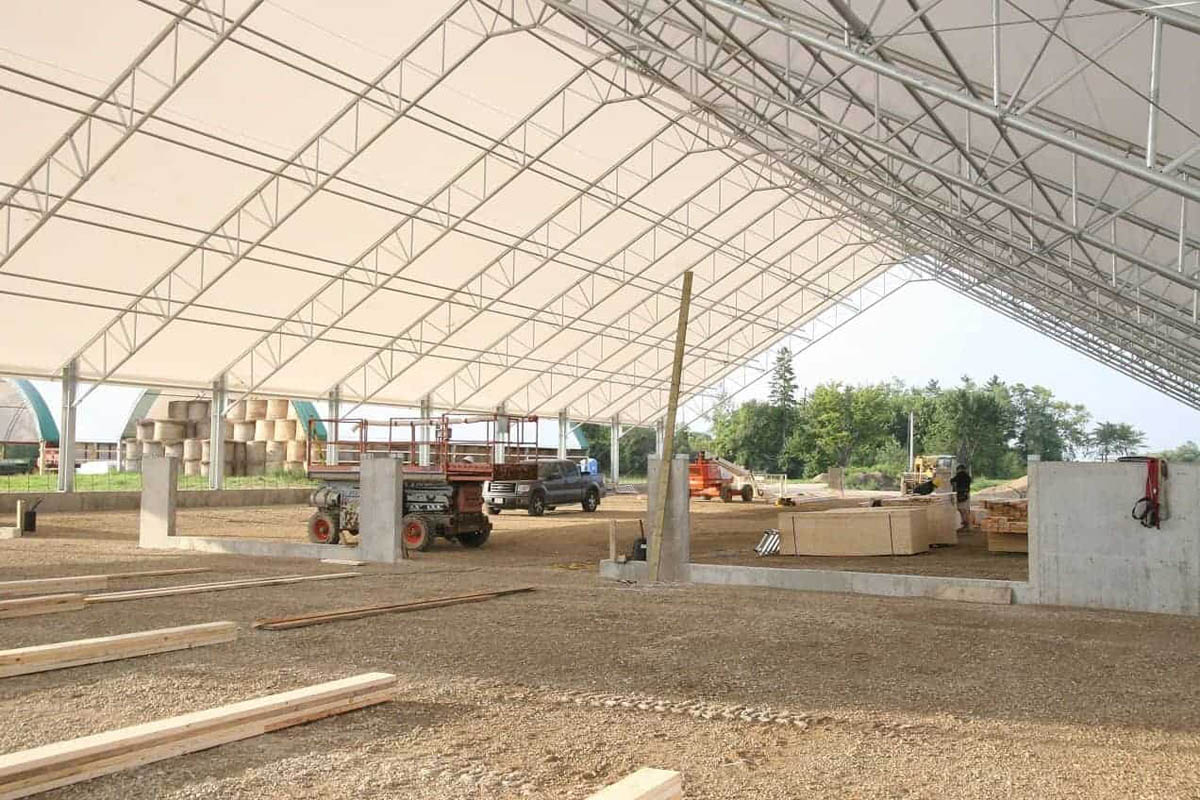
Today, there seem to be more and more building styles available when purchasing a structure, be it agricultural, commercial, or public works. Aside from conventional brick and mortar buildings, pre-engineered buildings and modular building systems are go-to options, often because of their speedy construction and versatile designs.
The most popular modular building styles are steel buildings and pre-engineered fabric buildings. But which one is right for you? That depends on your project and intended building use, and your bottom line – not just today but for the lifespan of the building.
Consider the speed of construction, building maintenance, and the lifespan of the roof system.
Speed of installation
Considering how long it will take to install your building is certainly something you want to think about. The longer the total construction timeline is, the higher the labor costs, and the longer your operating downtime. Operating downtime can affect the revenue you would normally be generating if the building was completed and performing its intended use.
Building construction will always vary depending on the foundation type, the building finishes, and special accessories like lighting, heating and cooling, hydro, plumbing, etc.
On average, a steel building will typically take twice as long as a fabric building to complete.
Where a steel building takes six weeks, and fabric building will likely take three to install, for example. This will include foundation installation, framework assembly, siding installation, and roof installation.
Many steel buildings and fabric buildings are pre-engineered and modular, so the framework will often go up quickly. The rest of the building finishes, notably the siding and roof installation, however, is where there is a difference.
Steel buildings require multiple sheets the are installed in sections using screws every so many feet, and at each joint.
Fabric buildings use durable covers that are pulled over an entire building, depending on the size, or quickly installed in panels. No screws or punctures to the roof while installing it.
Watch how quickly fabric covers are installed on this 65-foot-wide by 108-foot-long storage building.
Building maintenance
All building styles will require some form of maintenance. You will want to know ahead of time how much maintenance and the type of maintenance your building requires before purchasing it. These costs can add up over time and make the overall cost of your building more than you bargained for.
When fabric buildings are installed correctly, they are rigid and durable for decades.
Fabric buildings require very little maintenance. Accidentally get a tear or hole in your fabric? No problem, small patch kits make fast and easy repairs. If you ever require an entire panel or fully recover, they are easily replaced at a minimal cost.
Rusting or corrosion will never be a problem in a pre-engineered fabric building that has been hot-dip galvanized after all production. That means that lifelong corrosion protection was applied after all welding was completed.
Fabric covers have UV protection, and flame retardant properties.
Steel buildings can require much more maintenance over time, mostly due to the steel that starts to rust on every screw hole, as there is no insulation protecting the steel. UV rays from sun exposure wear down the plastic washers and eventually fall off, leaving the screw head exposed to deterioration.
This challenge alone leaves steel roofs exposed to more rusting in the future.
The owner of a steel building can expect to re-screw their steel roof a number of times during the lifespan of the building. This process can be a big hassle, as all the old screws must be removed, and a new larger screw with the new washer seal in its place. Lots of labor!
The cost of re-screwing a steel roof adds up and can be as much as replacing an entire fabric roof. Then an owner must consider repainting the roof on top of that, which typically needs to be redone every five years.
The lifespan of roof systems
Steel building manufacturers and resellers that use aluminum or steel roof systems boast roof lifespans of up to 50 years or longer. Sounds like a good investment! But, that lifespan has so many determining factors that it rules out a number of building applications.
Steel roof warranties exclude most agricultural applications and any commercial applications that are storing materials deemed as corrosive.
Corrosive materials include salt, any form of fertilizer, animal excrement, excessive humidity or moisture, etc. Because of these warranty limitations and exclusions, livestock barns, salt storage buildings, composting or fertilizer buildings, or maintenance and repair facilities are not ideal building applications. In addition, all forms of waste or recycling facilities should be avoided.
*Insulated buildings or additional protective barriers may change these limitations.
Fabric-covered buildings are known to last for over 20 years. No required repairs or recovers needed.
The polyethylene covers on a fabric building are non-corrosive, making them an excellent fit for any building application. Additionally, a fabric cover should not need to be replaced for 20 or so years, and at a fraction of the price of replacing an entire steel roof.
Other important considerations
All these factors when deciding between a steel building or a fabric roof are important and play a part in choosing the right fit for your application, operational needs, and your budget. Beyond the building install and longevity, buyers must think about the environment that the building will provide.
Steel framed buildings can be cost-effective and economical building solutions, making them appealing. However, there are several limitations pertaining to warranties and exclusions, building maintenance and maintenance costs, but also the environment inside the building due to the steel roof. For example, dark interiors with no natural light and poor ventilation.
This can leave buyers feeling stuck between a steel building and a fabric building.
With a steel roof, buildings tend to be darker and require quite a bit of additional daytime lighting and nighttime lighting. This additional lighting certainly adds to the operating costs of the building and takes away from the building’s return on investment.
Fabric buildings require no daytime lighting at all and provide naturally bright and shadow-free interiors until well into the evening. At night, the reflective properties of the fabric cover help disperse light from fewer units, saving on energy costs.
Building ventilation is important for any application, but particularly barns. Steel buildings tend to hold more moisture inside of a building, where the large interior airspace in a fabric building draws moisture up and away from livestock or stored materials.
The natural light and ventilation in a fabric building are reported to improve herd health, breeding cycles, and daily gains and production in livestock.
All Britespan’s customers have reported cooler, drier environments and more fresh air inside their fabric building when compared to their old steel buildings.
If the benefits of a fabric building sound like it’s right for you, contact us today for your free building estimate!