Six Essential Elements in Fabric Structure Development
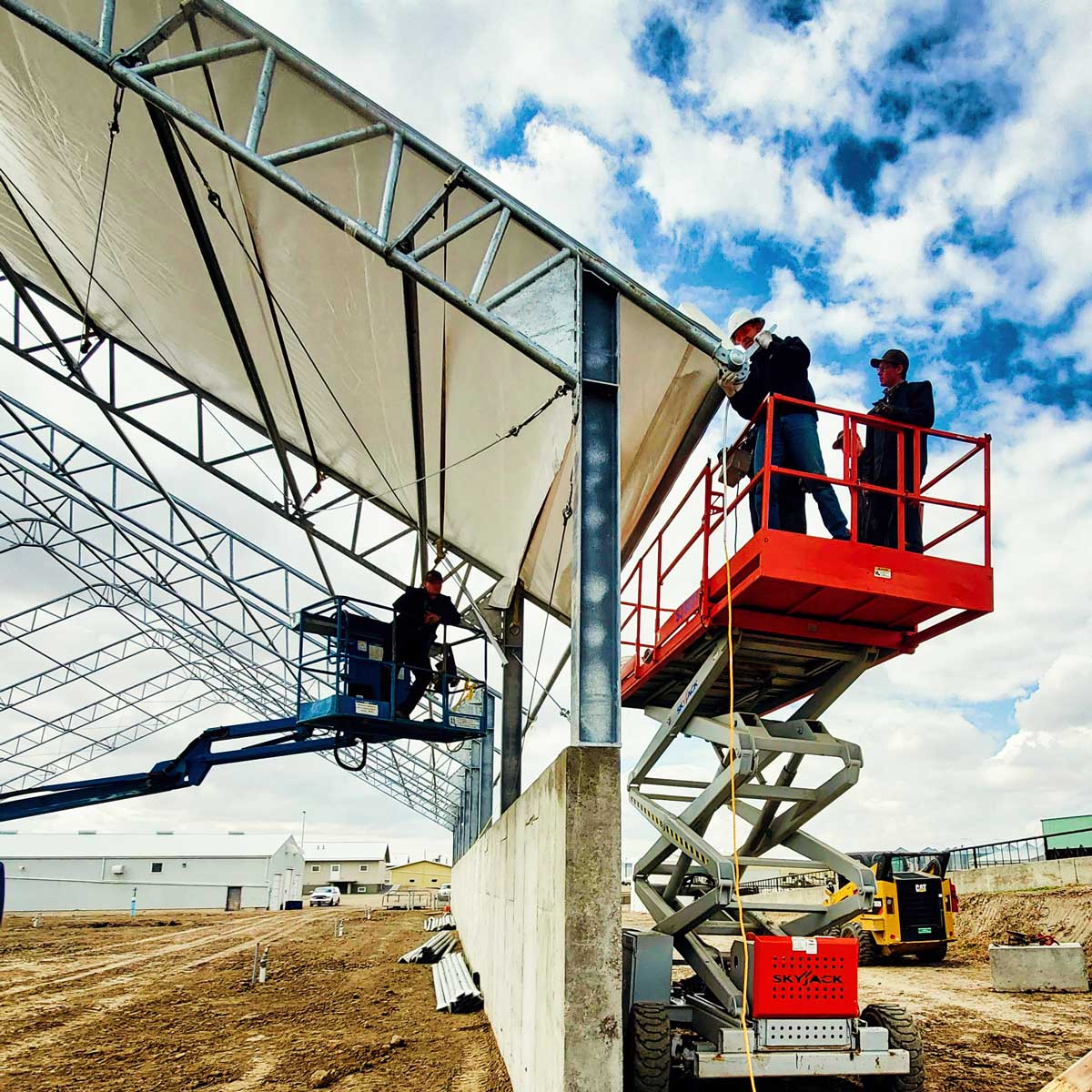
Searching for the perfect building solution that aligns with your unique requirements can often be a challenging journey. As you sift through various options, it becomes clear that Fabric Buildings, particularly those reinforced by a robust steel-frame and covered with a tensioned membrane cladding, stand out. This isn’t just because of their structural integrity, but also their adaptability. But when it comes to these innovative structures, there’s a lot more to understand than merely their available configurations, shapes, and sizes.
Those who have invested time in research and are well-versed with the intricacies of building solutions recognize that there are fundamental aspects to be considered. The crux of a successful fabric building project lies in recognizing and emphasizing six pivotal fabric structure elements in its development plan. These fabric structure elements often become the guiding principles for informed buyers, ensuring that they don’t just get a building but a solution that perfectly caters to their needs.
1. Engineering: A Foundation for Performance
The success and durability of any building fundamentally lie in its engineering. The very essence of a structure’s performance, its ability to withstand varying conditions, and its longevity can be traced back to the principles of solid structural engineering. Those who are well-informed and meticulous about their investments always probe deeper. They inquire about the very blueprints of their prospective buildings, seeking assurance that these plans have been curated and adapted for the unique conditions of their chosen site, and are not just generic designs.
A crucial aspect to consider, regardless of whether a building permit application is mandatory for your project, is the authenticity and credibility of the structural designs. It’s not just about having a drawing; it’s about having one that’s sealed and stamped by a professional engineer licensed and recognized in your specific state or province. This stamp is more than just a formality; it’s an affirmation of the building’s structural integrity and its compliance with local standards and conditions.
It’s worth noting that while some providers might offer structures without this rigorous engineering backing, it’s a risk. Such non-engineered buildings come without the assurance of performance, especially when faced with the diverse environmental conditions your site might present. The absence of a certified design can lead to unforeseen challenges, making it vital for potential buyers to prioritize engineering in their decision-making process.
2. Total Project Cost: A Holistic Understanding
When diving into a building project, understanding the complete financial picture is crucial. It’s not just about the visible or obvious costs; there are multiple layers to consider. Primarily, for the majority of construction ventures, three distinct cost centers play a pivotal role in determining the overall budget:
- The Building Package: This encompasses the tangible materials, designs, and building features that make up the structure.
- The Foundation: Often overlooked, this forms the base on which your entire building rests. Its quality and design are paramount to the structure’s stability and longevity.
- Labor Costs: The human resources employed not only influence the project timeline but also contribute significantly to the overall expenditure. From skilled laborers to specialists, their expertise comes at a price.
It’s vital to recognize that the type of building you choose can influence both the foundation expenses and the labor costs. A complex design might require a more intricate foundation or specialized labor, driving up costs. Thus, before settling on any particular building package, a deep dive into how these three cost centers intertwine and affect each other is essential.
Engage in a comprehensive discussion with your potential providers. Question them about possible synergies, efficiencies, and alternative options that could optimize costs across these areas. A golden piece of advice? Avoid fixating solely on the initial cost of the construction package. Instead, take a comprehensive approach to your project, ensuring you secure the most favorable financial and structural results. Consider various financing options to support your goals.
3. Life Expectancy: Beyond the Warranty Claims
The concept of life expectancy in buildings is one that goes much deeper than what’s often advertised. While many manufacturers prominently highlight extended warranty periods, there’s an underbelly of contingencies that one needs to be aware of. One critical factor, often lurking in the shadows, has the potential to either fortify or negate that warranty: the project design in relation to the specific conditions of the site.
Every construction site is unique, with its own set of environmental and geophysical challenges. If a building isn’t tailor-made for these particular conditions, it’s like placing a square peg in a round hole—it’s a recipe for disaster. Factors like corrosive atmospheres, heightened humidity levels, inadequate air circulation, and unfavorable soil conditions aren’t just minor impediments. They can be monumental challenges that severely truncate the life expectancy of a structure, rendering the warranty void.
So, what should a prospective buyer do? The answer lies in being proactive and informed. Rather than being swayed by lengthy warranty claims, delve deeper. Engage with providers and ask pointed questions about the strategies they’ve incorporated to ensure the building’s longevity, especially in the context of site-specific challenges. Ensure that these strategies are not only geared towards enhancing the building’s lifespan but are also in sync with the stipulations of factory warranties. In the world of construction, it’s not just about building for today but for decades to come.
4. Project Completion Timelines: The Speed Advantage
In the dynamic world of construction, time is often synonymous with money. This is where fabric buildings truly shine. Among the myriad of benefits they offer, their rapid deployment capability stands out prominently. Especially when dealing with extensive construction, the advantage of fabric structures becomes even more pronounced. It’s impressive how they can cut down the time from the initial order to the project’s final completion by a whopping 50%.
This expedited process doesn’t just mean a faster move-in or occupancy rate. When compared to other construction alternatives, the time efficiency of fabric structures offers tangible benefits. By completing projects in half the usual time, stakeholders can potentially witness cost reductions, given that prolonged construction often entails higher overheads and unforeseen expenses. Moreover, this swift execution means that the structure becomes operational sooner, paving the way for quicker returns on the investment made. In essence, when opting for industrial fabric buildings, one is not only choosing a building solution but also a pathway to efficiency and economic advantages.
5. Interior Clearances: The Often-Overlooked Essential
A commonly overlooked, yet crucial aspect in building design, is interior clearance. This seemingly subtle feature can make a world of difference in the day-to-day operations within a structure. Surprisingly, the primary cause for repair calls by building owners isn’t external wear and tear but rather internal impact damage. This is typically caused by operators and equipment inadvertently coming into contact with the building’s interior.
These accidents don’t just result in minor dents or scratches; they can lead to significant damage, requiring extensive and costly repairs. Given the frequency of such incidents and the associated repair costs, it becomes imperative for buyers to prioritize interior clearances right from the planning phase. Recognizing the significance of this aspect, it rightfully earns its place among the top six critical fabric structure elements.
Thankfully, modern architecture and design offer a plethora of options to address this concern. From designs that provide generous clearances along the sidewalls to those that ensure ample space in the building’s center, the choices are diverse. This flexibility ensures that the internal operations can proceed unhindered, minimizing the chances of accidental damage.
Wise buyers understand this intricate balance between space and safety. They realize that by allocating a portion of their budget to ensure appropriate interior clearances, they’re making a long-term investment. This foresight not only guarantees a safer operational environment but also translates into significant savings in potential repair costs in the future. A spacious and well-planned interior is not just about comfort; it’s a critical component of a building’s longevity and efficiency.
6. The Power of Using Factory-Authorized Dealers
When embarking on any construction project, one of the critical decisions to make revolves around who you trust with the installation. This is where the importance of factory-authorized dealers comes to the fore. If the pillars of quality, reliability, and accountability are paramount to you, then the triad of the customer, dealer, and manufacturer becomes indispensable.
This synergy isn’t by accident. Dealers and manufacturers consciously form a partnership, anchored in their mutual commitment to excellence. Their united objective is clear: to deliver the finest products and services tailored to the customer’s needs. Moreover, authorized dealers undergo rigorous training directly from the manufacturers. This specialized training ensures that they are adept at installing fabric buildings, ensuring every procedure aligns with the manufacturer’s stringent guidelines. This alignment guarantees safety, ensures the building’s durability, and promises optimal performance.
While the allure of potential savings might tempt some to bypass authorized dealers and opt for a direct purchase, followed by contracting an unfamiliar installation team, this path is fraught with risks. Such shortcuts might seem economical at first glance, but the potential pitfalls and challenges can eclipse the initial savings. Whether it’s the risk of incorrect installations, compromised safety, or reduced longevity of the structure, these are costs no owner wants to bear.
Buyers, armed with this knowledge, prioritize the long-term advantages over short-lived savings. They understand that collaborating with manufacturer-authorized dealers isn’t just a choice – it’s the most strategic, secure, and efficient route to realizing their construction aspirations.
In conclusion, while the prospect of setting up a fabric building can seem daunting, by focusing on these six crucial fabric structure elements, you can ensure that your project not only meets but exceeds expectations. It’s about making informed decisions, understanding the nuances of your specific project, and partnering with the right professionals who can guide and execute your vision to perfection.